Home > Company News > How to improve the service life of grinding wheel
Company News
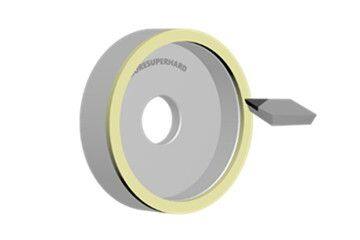
1.Abrasive coating of resin bonded grinding wheel
Super hard abrasive coatings are most commonly used on resin-bonded grinding wheels, while nickel and copper are the preferred coating materials. Coating thickness depends on coating material. Copper coating usually accounts for 50 % of the total weight of coated abrasive particles. Nickel coatings accounted for 30, 56 or 60 percent of the total weight of the coated grains. The 56 nickel coating has a stronger grain holding force (longer holding time), but it also generates more heat. Silver can also be used as a grainy coating for resin-bonded grinding wheels, which, despite its high cost, has the desired lubrication properties. The silver-coated super hard grinding wheel is mainly used to grind the spiral groove of the cemented carbide drill bit.
2.Abrasive coating of metal and vitrified bonded grinding wheel
The coating used for metal-bonded grinding wheels is metal-carbide base coating. The most common coating materials are titanium carbide and chromium carbide. The metal-carbide-based coating can also protect diamond abrasive particles from adverse reactions between abrasive particles and binder that may occur during grinding wheel manufacturing. The super hard abrasive coating in the ceramic bonding wheel is titanium, In the metal-bonded grinding wheel, the coating protects the diamond grain from the influence of the bond system. In ceramic bond grinding wheel, coating is to protect the bond system from the influence of CBN abrasive particles. Coating on the abrasive particles with titanium carbide coating can effectively improve the wettability of the abrasive particles and increase the control force.
3.Defects of abrasive coatings
The only potential drawback to using coated abrasive super abrasive wheels may be the increased cost. In most cases, grain-coated super hard abrasive wheels perform better than uncoated wheels (although there are exceptions). If the grinding wheel manufacturer does not improve the binder to take full advantage of the coating's performance, the end user may not be able to see the difference between coating and non-coating when the binder and coating are designed as an integral system for the best results.
-
sponge grinding wheel for stainless steel
-
diamond polishing pad for marble and granite
-
abrasive Sheet Roll
-
Brazed PCBN Inserts, Soldering PCBN Inserts
-
Solid CBN Inserts for Hard Turning Cast Iron and Hardened Steel
-
DEERFOS PZ533 polishing 300 and 304 stainless steel, alloy steel, aircraft propellers and helicometers
-
Diamond stone tool 100mm abrasive disc grinding wheel flexible polishing pad
-
10pcs Blade grinding plate polishing metal stainless steel 100 Angle grinding machine grinding wheel Angle polishing plate
-
CBN Honing Cylinder Engine Block Diamond Honing Stones
-
H70/H50 Honing Stone,Honing tools
-
Li-Battery Electric Railway Grinding Machine/ Rail Grinder
-
NCM-5.1 Frog and Switch Point Grinder
-
NGM-6.0 Rail Profile Grinder
-
Electroplated diamond bit
-
compact bit
-
Single Crystal Diamond Milling Tools
-
Single Crystal Diamond Turning Tools
-
Polish Master Tools
-
OHIO Engraving Stylus
-
HELL Engraving Stylus with Wing (4K)
-
High precision electric spindle CBN grinding wheel grinding rod 20Cr carburizing quenching inner circular grinding machining
-
Customized processing of carbon fiber with irregular shaped steel sand grinding head profile for rapid prototyping with good roughness
-
Customized 190mm long electroplated diamond sand needle SDC120 # for drilling wood with a handle diameter of 2.5mm
-
Customized Round Head Diamond Resin Grinding Rod R15 Semiconductor Ceramic Precision Grinding 32mm Straight Shank Arc SDC140 Mesh